Introduction: an overview of TDP tablet presses and the need for TDP molds customization
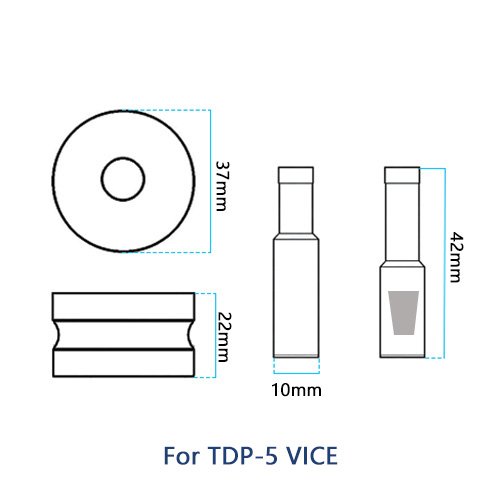
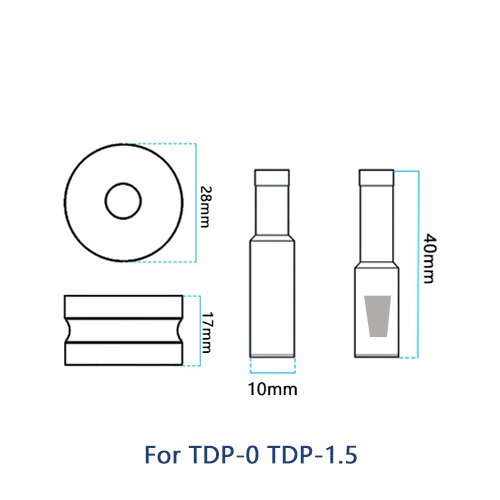
Tablet presses are devices that help manufacturers produce tablets with a desired shape and size. Tablet presses can also be used to create other types of products, such as vitamin and fitness tablets.
The need for TDP molds customization arises because tablet presses typically have different pressing requirements than other types of manufacturing machines. For example, tablet presses require a high degree of accuracy when pressing the tablets into the desired shape. This is why it is important for manufacturers to have access to TDP molds that perfectly fit their specific needs.
There are many different brands of pill press die on the market, each with its own set of features and specifications. As a result, it can be difficult for manufacturers to find a press that precisely meets their needs.
Unique TDP molds designs: what makes them different?
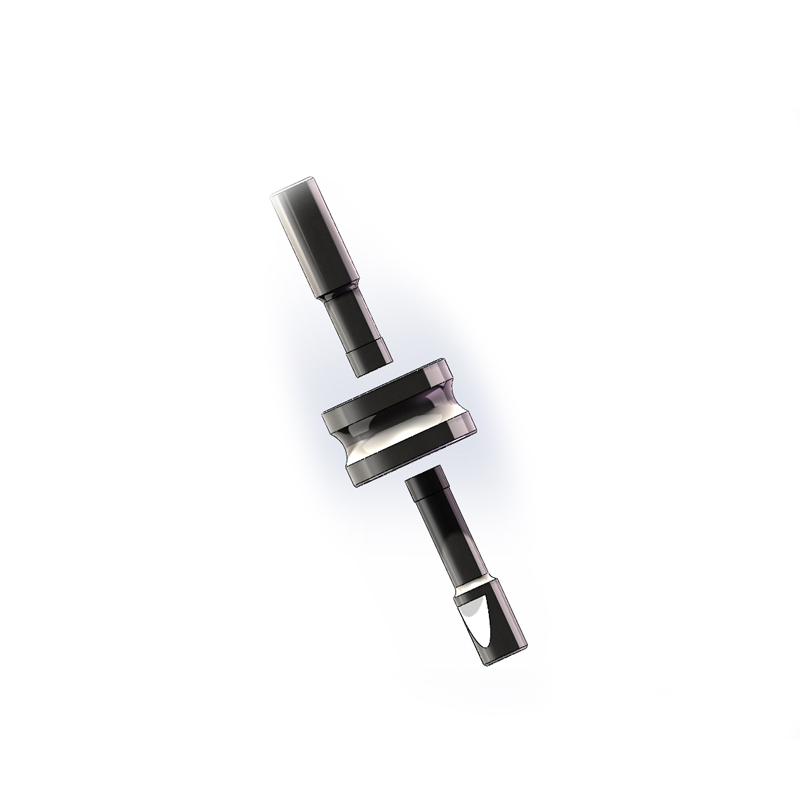
Tablet Press Molds: What Sets Them Apart?
There is a variety of different TDP punch die molds designs on the market, each with its own unique features that set it apart from the others. Some of these unique designs include TDP pill press molds, which are specifically designed to produce tablets quickly and easily. Here are some of the reasons why these pill press molds are so popular:
-They’re Compact: TDP pill press molds are small and easy to transport, making them perfect for use in small businesses or homes.
-They’re Fast: Because TDP pill press molds use minimal heat and pressure, they create tablets quickly and easily. This speeds up the production process by eliminating the need for lengthy dry periods between batches.
Ease of use and quick changeover: benefits for manufacturers
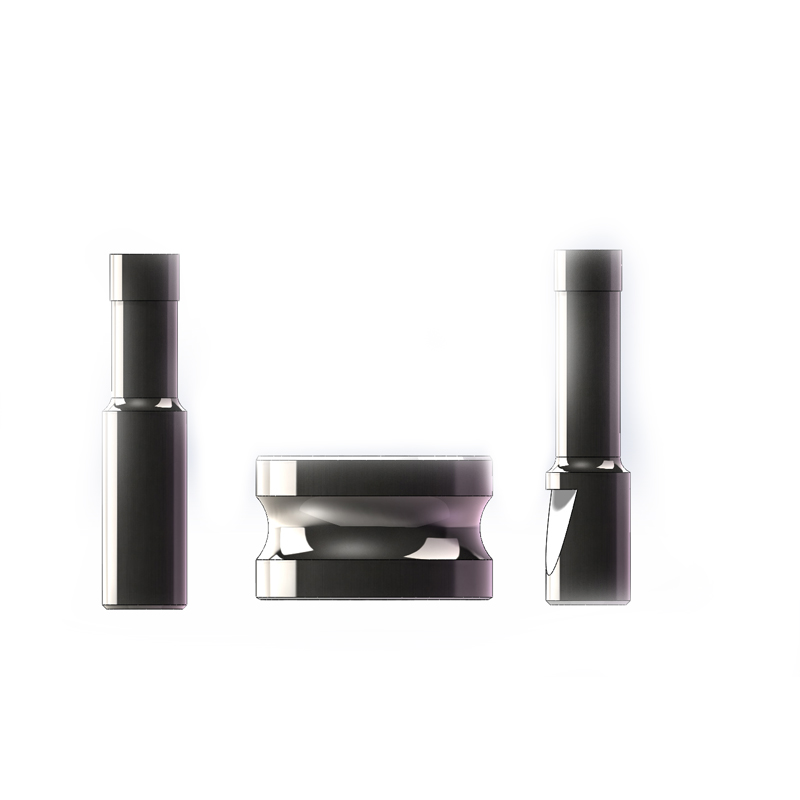
Manufacturers that use TDP molds for press molding often find that the ease of use and quick changeover benefits them in several ways. First, because TDP tablets are easy to handle, the manufacturing process is quicker and less error-prone. Second, since the molds can be changed quickly and easily, production can continue uninterrupted even if a part becomes damaged or defective. Finally, with TDP tablets making up a smaller percentage of the overall manufacturing cost, manufacturers can save money by using them instead of more expensive methods.
Manufacturing companies that produce tablets and other mobile computing devices face increased demand for products with high throughput. This has led to a rise in the use of tablet presses, which are machines that can quickly and easily change molds for different types of tablets. Tablet presses reduce the amount of time it takes to produce different types of tablets, making them more appealing to consumers. Manufacturers can also save money by using tablet presses, as they do not have to spend as much on new molds.
Manufacturers face a dilemma when it comes to tablets. On the one hand, there is the desire to create new, innovative designs that are both visually appealing and functional. On the other hand, manufacturers must consider how easy it is for their technicians to change over from one tablet design to another without losing any valuable production time.
One solution is to use a TDP (Tablet Press Mold) – a machine that allows for quick changeover between tablet press molds. This not only eliminates wasted time and resources but also helps ensure that each tablet press mold is used as intended and produces high-quality products.
Variety of applications: a wide range of possibilities
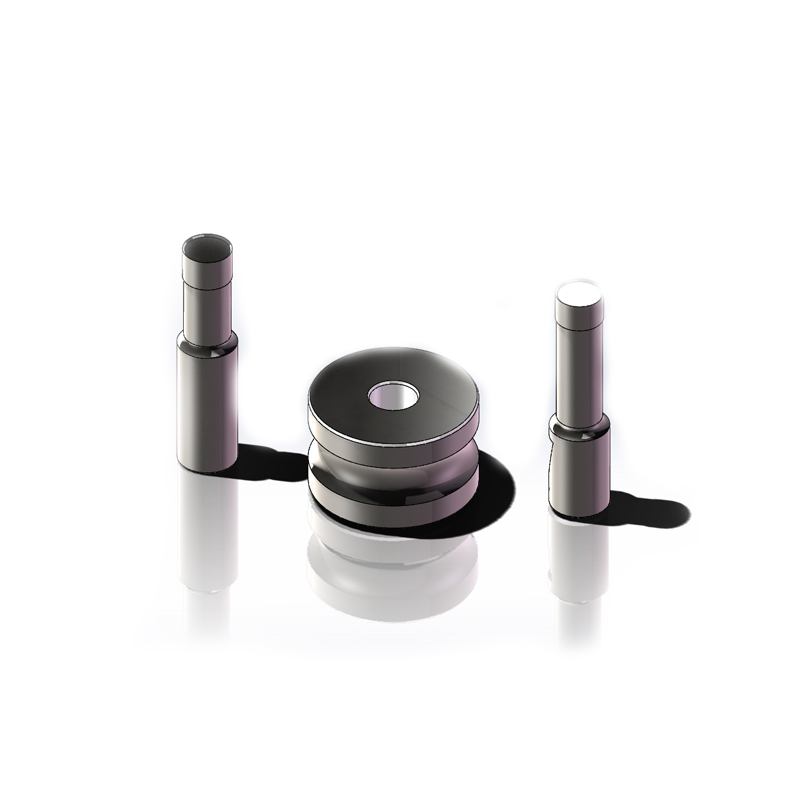
In today’s market, there are a wide variety of applications that can be used with a tablet press. Depending on the design and specifications of the tablet press, different molds can be made. This allows for a variety of products to be produced, such as food containers, gaming controllers, and even prosthetic devices. With so many possibilities available, it is important to choose the right tablet press for the job at hand.
Quality and accuracy: precision components for perfect results
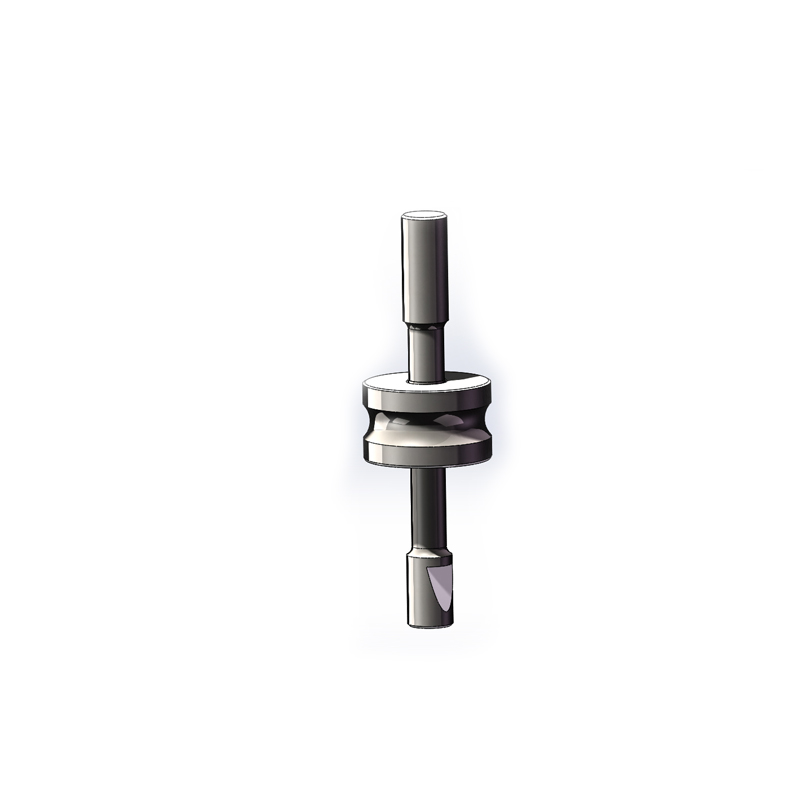
Manufacturing a product to specification is the key to achieving perfect results. This is why precision components are so important in tablet press molds – they ensure that every part of the product is precisely formed, resulting in quality prints and products.
TOPTDP offers a wide range of precision components for use in tablet press molds, ensuring that you can produce products with the best possible accuracy and quality. Our components are manufactured with the highest standards of precision, ensuring that you get the best possible results from your press. With TOPTDP’s precision components, you can be sure that your products will meet all your specifications – and deliver exceptional quality and results!
Customer service and support: always there to help
Customer service and support are a cornerstone of any business. It is important to ensure that customers have the resources they need to get their issues resolved and that the company always has staff available to assist them. Tablet press molds are a great example of a product that relies heavily on customer service and support.
When users buy a tablet press mold, they rely on the company to provide them with a product that will produce high-quality parts. If something goes wrong with the mold, it is important for the company to be able to provide support for its customers. This means having staff available who can help users troubleshoot their issues, provide replacement parts, or even refund their purchase if necessary.
It is crucial for companies like this to have an adequate customer service infrastructure in place because it ensures that users have the resources they need when they need them.